Ceb-fip Model Code 2010 Free Download
The fib Model Code 2010 is now the most comprehensive code on concrete structures, including their complete life cycle: conceptual design, dimensioning, construction, conservation and dismantlement. It is expected to become an important document for both national and international code committees, practitioners and researchers. Members using the fib. Pdf Ceb fip model code 2010 WordPress com. Wiley fib Model Code for Concrete Structures 2010 fib. Finite element modeling incorporating non linearity of. Fib Model Code 2010 Seminar VCE. 12 1 2 CEB FIP Model Code 2010 Analysis and Design. DESIGN OF STEEL FIBRE REINFORCED CONCRETE BEAMS USING THE 1 / 13.
- Ceb-fip Model Code 2010 Free Download Crack
- Ceb-fip Model Code 2010 Free Download Windows 7
- Ceb-fip Model Code 2010 Free Download Utorrent
- Ceb-fip Model Code 2010 Free Download For Windows
- Ceb-fip Model Code 2010 Free Download 64-bit
- Ceb-fip Model Code 2010 Free Download For Pc
Fib model code for concrete structures (eBook, ) [donkeytime.org]
Model Code 2. Final draft, Volume 1. Title: Model Code 2. Category: Model Code. Year: 2. Format approx.
Ceb-fip Model Code 2010 Free Download Crack
fib MC2010 - Design rules for FRC and applications
The fib Model Code is now the most comprehensive code on concrete structures including their complete life cycle.
For reinforced concrete structures, as beams, slabs or walls, failure under bending is well known and its description and design is relatively internationally agreed. However for the shear failure phenomenon, there is not yet a common agreement at the international level, no consensus is reached on the subject at this time. Many parameters are involved in the shear resistance mechanism and many phenomena coexist. The shear force transfer mechanisms are sometimes complex and difficult to discern. By analyzing the different shear design codes, some shear parameters are taken into account and ignored by others, which makes that a shear effect may be omitted. In addition, different ways are adopted to take into account the different shear parameters.
Description
In some cases, such as punching in ULS where specific fracture determines behavior, models may be affected by greater uncertainty, which can be explained by adding a specific factor in the verification formulas. - If you do not receive an email within 10 minutes, your email address may not be registered, and you may need to create a new Wiley Online Library account. If the address matches an existing account you will receive an email with instructions to retrieve your username.
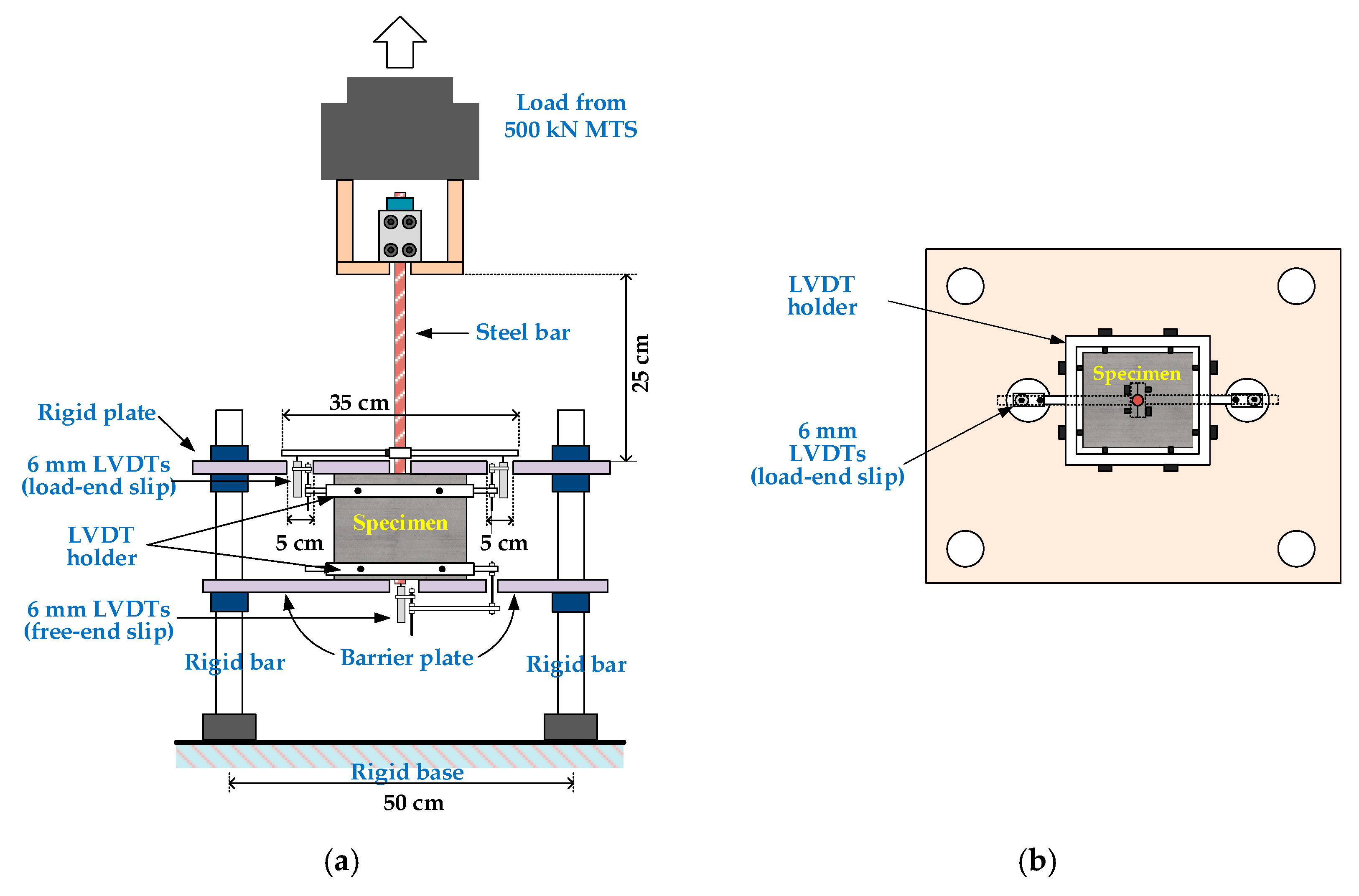
Ceb-fip Model Code 2010 Free Download Windows 7
Ebook Library. John Wiley. ProQuest Ebook Central. Please choose whether or not you want other users to be able to see on your profile that this library is a favorite of yours. Finding libraries that hold this item You may have already requested this item.
The organization depends on the voluntary contributions of international experts to achieve its mission and plays a role in stimulating research and promoting the use and development of concrete. Today this office is the headquarters of the fib. The fib continues the work of its founding associations by providing technical reports, state-of-the-art reports, manuals, textbooks, guides, recommendations and model codes. There are forty-five national member groups NMGs in the fib. They act as forums for co-operation and coordination. The general assembly deals with high-level administrative and technical matters, such as elections, finances, statutes and the approval of model codes. The technical council TC oversees the work of the commissions and task groups.
Ceb-fip Model Code 2010 Free Download Utorrent
Ceb-fip Model Code 2010 Free Download For Windows
Ceb-fip Model Code 2010 Free Download 64-bit
bookCeb-fip Model Code 2010 Free Download For Pc
March 2010
232
6 Interface characteristics
Explicit consideration of the influence of bond on performance at the serviceability limit state and on rotation capacity is not normally required for members reinforced with conventional plain or deformed steel bars. The influence is instead represented by a modification of the tension stiffening from surrounding concrete.
6
Interface characteristics
6.1
Bond of embedded steel reinforcement
Bond is the term used to denote the interaction and transfer of force between reinforcement and concrete. Bond influences performance of concrete structures in several ways. At the serviceability limit state, bond influences width and spacing of transverse cracks, tension stiffening and curvature. At the ultimate limit state, bond is responsible for strength of end anchorages and lapped joints of reinforcement, and influences rotation capacity of plastic hinge regions.
6.1.1
Local bond-slip relationship
The bond stress-slip relationship depends on a considerable number of influencing factors like rib geometry (related rib area), concrete strength, position and orientation of the bar during casting, state of stress, boundary conditions and concrete cover.
Under well-defined conditions, it is possible to consider that there is an average 'Local bond' versus 'Local slip' relationship, for short anchorage lengths, statistically acceptable.
Therefore the bond stress-slip curves for confined and unconfined concrete, presented in Figure 6.1-1, can be considered as statistical mean curves, applicable as an average formulation for a broad range of cases. Further reliability handling would be needed to derive design bond stress-slip curves.
For monotonic loading the bond stresses between concrete and reinforcing bar for pull-out and splitting failure can be calculated as a function of the relative displacement s according to Eqs. (6.1-1) to (6.1-4) (see Figure 6.1-1).
The first curved part refers to the stage in which the ribs penetrate into the mortar matrix, characterized by local crushing and micro-cracking. The horizontal level occurs only for confined concrete, referring to advanced crushing and shearing off of the concrete between the ribs. This level represents a residual bond capacity, which is maintained by virtue of a large concrete cover or a minimum transverse reinforcement, keeping a certain degree of integrity intact. The decreasing branch refers to the reduction of bond resistance due to shearing of the concrete corbels between the ribs. In case of unconfined concrete splitting failure occurs which is reflected by a sudden drop of the bond strength before the horizontal level is reached.
τ0 = τmax (s/s1) α
for
0 ≤ s ≤ s1
(6.1-1)
τ0 = τmax
for
s1 ≤ s ≤ s2
(6.1-2)
τ0 = τmax (τmax - τf ) (s-s2)/(s3-s2)
for
s2 ≤ s ≤ s3
(6.1-3)
τf
for
s3 < s
(6.1-4)
With regard to the generation of bond stresses, the following considerations apply. Reinforcement and concrete have the same strain (εs = εc) in those areas of the structure where the steel is under compression and in uncracked parts of the structure under tension. In cracked cross-sections the tension forces in the crack are transferred by the reinforcing steel. In general, the absolute displacements of the steel us and of the concrete uc between two cracks or along the transmission length lt are different. Due to the relative displacement s = u s-uc bond stresses are generated between the concrete and the reinforcing steel. The magnitude of these bond stresses depends predominantly on the surface of the reinforcing steel, the slip s, the concrete strength fck and the position of the reinforcing steel during concreting. Between cracks or along the transmission length lt a part of the tension force of the reinforcing steel, acting in the crack, is transferred into the concrete by bond (tension stiffening effect). The local decrease of the relative displacement along the transmission length lt, is characterized by the strain difference: ds/dx = εs - εc Depending on the selection of the coefficient α (0 ≤ α ≤ 1) in Eq. (6.1-1) all usual forms of a bond stress-slip relationship can be modelled, starting from a bond characteristic with a constant stress (α = 0) up to a bond stressslip relationship with linear increasing bond stress (α = 1). The parameters given in Table 6.1-1 are valid for ribbed reinforcing steel with a related rib area Asr ≈ Asr,min according to relevant international standards. Depending on the failure mode, pull-out or splitting, different parameters are applied. In order to take other bond conditions into consideration a further distinction of the parameters is made.
fib Bulletin 55: Model Code 2010, First complete draft – Volume 1
233
234
6 Interface characteristics
Table 6.1-1:
1
2
3
4
5 Splitting (SP)
εs < εs,y
εs < εs,y
All other Good bond cond. bond unconfined stirrups cond. 0.25
Splitting
τu,split1 stirrups
All other bond cond. unconfined 0.25
Pull -Out
τu,split 2
&f # 5.0 ' $ ck ! % 20 '
0.25
stirrups &f # 5.5 ' $ ck ! % 20 '
0.25
τ max 2.5√fck
1.25√fck
&f # 7.0 ' $ ck ! % 20 '
s1
1.0mm
1.8mm
s(τmax)
s(τmax)
s(τmax)
s(τmax)
s2
2.0mm
3.6mm
s1
s1
s1
s1
s3
cclear 1)
cclear1)
1.2s1
0.5cclear1)
1.2s1
0.5cclear1)
α
0.4
0.4
0.4
0.4
0.4
0.4
τf
0.40τmax
0.40τmax
0
0.4τmax
0
0.4τmax
1)
&f # 8.0 ' $ ck ! % 20 '
τmax
6
Pull-Out (PO)
Good bond cond.
τ
Parameters for defining the mean bond stress-slip relationship of deformed bars (acc. to Eqs. (6.1-1) to (6.1-4))
cclear is the clear distance between ribs
The values in Table 6.1-1, columns 1 and 2 (pull-out failure) are valid for well confined concrete (concrete cover ≥ 5 Ø, clear spacing between bars ≥ 10Ø). The values in Table 6.1-1, columns 3 to 6 (splitting failure) are valid for Ø ≤ 20mm, cmax/cmin = 2.0, cmin = Ø and Ktr = 2% in case of stirrups. For definition of Ktr see Eq. (6.1-5).
unconfined
τf Slip s s1
Figure 6.1-1:
s2
s3
Analytical bond stress-slip relationship (monotonic loading)
'u,split
#f $ = (2 ) 6.54 ) * ck + - 20 .
0.25
# 20 $ )* + -,.
0.2
!# c $0.33 # c $0.1 ' % ) * min + ) * max + + 8K tr & %/- , . &0 - c min .
(6.1-5)
where: η2
= 1.0 for good bond conditions, = 0.7 for all other bond conditions
fck
is characteristic cylinder concrete compressive strength (N/mm²)
Ø
is diameter of the bar (mm)
cmin = min{cx,cy,csi} cmax = max{cx, csi} and Ktr = nl Asv/(nb Ø sv) where: nl
is number of legs of confining reinforcement at a section
Asv is cross sectional area of one leg of a confining bar [mm²] sv
= longitudinal spacing of confining reinforcement [mm]
nb
= number of anchored bars or pairs of lapped bars
Ø
is diameter of the anchored bar or of the smaller of a pair of lapped bars [mm]
For those parts of the reinforcing bar which are at a distance x ≤ 2 Ø from a transverse crack, the bond stress τ and the slip s are to be reduced by the factor λ where: λ = 0.5 x/ Ø ≤ 1
fib Bulletin 55: Model Code 2010, First complete draft – Volume 1
(6.1-6)
235
236
6 Interface characteristics
The bond stress-slip curve is considerably influenced by reinforcement yielding and by transverse pressure. Taking into account these phenomena the bond stress according to Eqs. (6.1-1) to (6.1-4) should be modified by the factor Ωy in case of bar yielding and Ωp,tr in case of lateral pressure:
τbm = τ0 ⋅ Ωy ⋅ Ωp,tr
(6.1-7)
where:
τbm is bond stress according to the modified bond stress-slip curve τ0
is bond stress according to the bond stress – slip curve defined by Eq. (6.1-1) to (6.1-4)
If yielding of reinforcement occurs along the embedment length, the corresponding reduction of the bond stress is given by the factor Ωy according to Eq. (6.1-8).
! y = 1.0 b
# y = 1.0 ! [0.85 ' (1 ! e !5 a )
for εs ≤ εsy
(6.1-8a)
for εsy < εs ≤ εsu
(6.1-8b)
with
a=
Figure 6.1-2:
Influence of steel strains on local bond-stress slip relationship in case of pull-out failure
! s ' ! sy ! su ' ! sy
& f # ; b = $2 ' t ! f y !'
%$2
(6.1-8c)
If transverse pressure is present the bond stress slip curve for pull-out failure should be modified by the factor Ωp,tr according to Eq. (6.1-9).
' p,tr = 1, 0
for #c $ 0
(6.1-9a)
% ' # (& ' p,tr = 1, 0 ) tanh ,0.2 * . ! / 0 0,1 * f c 1 3 2
for #c + 0
(6.1-9b)
where '! is the mean compressive stress (orthogonal to the bar axis) averaged over a volume around the bar with a diameter of 3 Ø. fc is the mean concrete compressive strength. Figure 6.1-3:
Influence of transverse pressure on local bond-stress slip relationship in case of pull-out failure
The parameters given in Table 6.1-2 are valid for smooth reinforcing steel, depending on the main influencing factors: roughness of the bar surface, bond conditions and concrete strength. They are valid for confined and unconfined concrete. They are applicable only in loading states for which the concrete is not subjected to lateral tension, in the elastic range of the reinforcement and for those parts of the reinforcing bar with the distance x > 2Ø from a transverse crack. For those parts of the reinforcing bars with a distance x ≤ 2Ø from a transverse crack, the bond stress τ and the slip s are to be reduced by the factor λ according to Eq. (6.1-6)
If there is any tension stress around the bar then Ωc=1,0.
!max
Unloading branch
! = !max(s/s 1)' S !f s1
Figure 6.1-4:
fib Bulletin 55: Model Code 2010, First complete draft – Volume 1
s2
s3 Slip, s
Unloading branch of the τ-s relationship
237
238
6 Interface characteristics
Table 6.1-2:
Parameters for defining the bond stress-slip relationship of smooth bars (according to Eqs (6.1.-1) to (6.1.-4)) Cold drawn wire
s1 = s2 = s3
α
τmax=τf
Hot rolled bars
Good bond conditions
All other bond cond.
Good bond conditions
All other bond cond.
0.01mm
0.01mm
0.1mm
0.1mm
0.5
0.5
0.5
0.5
0.1√fck
0.05√fck
0.3√fck
0.15√fck
The unloading branch of the bond stress-slip relationship is linear and valid for the increasing and horizontal part of the diagram. The slope S (see Figure 6.1-4) is independent of the slip value s, and has an average value of S = 200 N/mm³.
The parameters given in Tables 6.1-1 and 6.1-2 are mean values. It has to be kept in mind that the scatter of different test series is considerable, especially for small values of slip. For a given value of the slip the coefficient of variation of the bond stresses may amount to approx. 30%. The scatter is due to the use of different test specimens and the resulting differences in the state of stress in the concrete surrounding the reinforcing bar, to the different measuring techniques, and to the different loading and deformation velocities. The heterogeneity of the concrete and the geometry of the reinforcing bars (related rib area, diameters) also have a significant influence on the τ - s relationship. The designer should take account of this scatter as far as possible, at least in the cases where a more accurate design is necessary.
6.1.2 Rules for serviceability behaviour have been derived for ribbed bars with a relative rib area fr within the range 0.05-0.07. More highly ribbed bars may be capable of developing higher bond stiffness, while coatings may cause a reduction. Coefficients β representing the influence of bond in Eqs. (7.6-5) and (7.6-17) in clause 7.6 may be modified in proportion to measured bond stiffness. In the absence of test data, the β coefficient for plain round and for epoxy coated ribbed bars should be taken as 50% of that for a ‘normal’ ribbed bar.
Influence on serviceability
The influence of bond on crack control and tension stiffening may be estimated from the secant modulus of local bond-slip behaviour measured in accordance with RILEM pullout test procedures at a free end slip of 0.01mm.